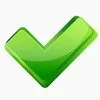
Перспективы развития керамзита для производства эффективных легких бетонов
В настоящее время в стране наблюдается тенденция к вытеснению керамзита и замене его другими видами утеплителей при производстве наружных ограждающих конструкций. Дело в том, что практически весь выпускаемый по России керамзит имеет среднюю насыпную плотность порядка 550 кг/м³. Однако в новых условиях, связанных с повышением требований к термическому сопротивлению наружных стеновых панелей, производство однослойных панелей в прежнем виде, даже при всех новациях, на рядовом керамзите не представляется возможным.
С другой стороны, использование керамзита при изготовлении конструкционного бетона так же представляется проблематичным. Стоимость керамзита из-за высоких энергетических затрат на его производство практически всегда будет выше стоимости щебня, а поэтому большинство несущих конструкций проектируется и производится из тяжелого бетона.
Все выше сказанное объясняет резкое снижение объемов производства керамзита по всей стране.
Однако нельзя не считаться с другой реальностью — в России создана мощная база керамзитовой продукции (построены десятки заводов, созданы и работают коллективы высококвалифицированных специалистов и т.п.). В этих условиях ликвидацию керамзитовой промышленности нельзя признать правильным решением.
На наш взгляд, в современных условиях следует видоизменить свойства керамзита, выпускаемого на керамзитовых заводах, и определить основные пути его возможного применения.
Одним из путей решения данной проблемы является организация производства особо легкого керамзита с насыпной плотностью 150-200 кг/м³. На этом керамзите возможно производство однослойных наружных стеновых панелей, удовлетворяющих новым требованиям по теплозащите и энергосбережению. Однако толщина этих панелей на обычном керамзитобетоне на керамзитовом песке составит порядка 70 см при термическом сопротивлении 3,2 (м² ºС)/Вт при средней плотности бетона 600 кг/м³ и расчетном коэффициенте теплопроводности бетона 0,20 Вт/(м ºС) при влажности бетона 5% (теплопроводность бетона в сухом состоянии — 0,16 Вт/(м ºC). Для понижения теплопроводности наружных стеновых панелей наиболее эффективным методом в настоящее время является способ поризации керамзитобетонных смесей.
Кафедрой «производство строительных материалов, изделий и конструкций» Самарской государственной архитектурно-строительной академии разработана принципиально новая технология приготовления беспесчаных керамзитопенобетонных смесей и изготовления из них однослойных наружных стеновых панелей с улучшенными теплотехническими характеристиками (патент РФ N 2059587 «Способ приготовления керамзитопенобетонной смеси», Бюлл. N 3 за 1996 г., авторы — Комиссаренко Б.С. и Чикноворьян А.Г.).
Эффективность данной технологии обусловлена применением нового устойчивого синтетического пенообразователя ПО-6К (производства ПО «Салаватнефтеоргсинтез»). При этом для приготовления керамзитопенобетонов возможно использование стандартного оборудования практически без его переделки. Мелкий заполнитель полностью исключается из состава бетона.
Особо следует отметить, что разработанные беспесчаные керамзитопенобетоны имеют слитную структуру цементного камня, насыщенную множеством мельчайших замкнутых воздушных пор. Такое строение является весьма эффективным с точки зрения теплозащиты. Коэффициент теплопроводности беспесчаных керамзитопенобетонов, изготовленных по данной технологии, на 0,3-0,4 Вт/(м ºC) ниже, чем у керамзитобетонов на керамзитовом песке и керамзитопенобетонов, изготовленных на традиционных пенообразователях (клее-канифольном, смоло-сапониновом, нейтрализованной гидролизной боенской крови животных — ПО-6 и т.п.) за счет снижения средней плотности бетона на 250-300 кг/м³.
Технология поризации беспесчаных керамзитопенобетонов, а также уникальные глины Самарской области, позволяющие в промышленных условиях (например, на ОАО «Легкий керамзит», г.Самара) получать керамзитовый гравий с насыпной плотностью 150-200 кг/м³, дают возможность изготавливать беспесчаный керамзитопенобетон со средней плотностью в сухом состоянии 650-700 кг/м³, с коэффициентом теплопроводности сухого бетона не более 0,14 Вт/(м ºС) и расчетным коэффициентом теплопроводности бетона не более 0,16 Вт/(м ºС) — при сухих и нормальных влажностных режимах эксплуатации помещений в сухой климатической зоне влажности (условия г.Самары).
Расход материалов на 1 куб. м керамзитопенобетона М50 составляет: цемента — 250-300 кг/м³; керамзита — 1150-1250 л/м³; воды — 140-160 л/м³; добавки ПО-6К — 1,5 % от массы цемента.
Максимальное насыщение керамзитопенобетона, поризованного пеной, крупным пористым заполнителем при использовании особо стойких технических пенообразователей обеспечивает ему минимальные плотность и коэффициент теплопроводности. Благодаря пластифицирующему действию технической пены расход воды затворения снижается до l50 л/мº и менее, а производственная влажность изделия — до 13% по объему и менее.
Применение керамзитопенобетона позволит уменьшить толщину однослойной стеновой панели до 50-55 см за счет снижения расчетного коэффициента теплопроводности бетона до 0,16 Вт/(м ºС).
На нашей кафедре накоплен достаточный положительный опыт при внедрении керамзитопенобетона. Так, в 1995-1996 гг. производство керамзитопенобетона для наружных стеновых панелей было организовано на ряде заводов Самарской области (АО «ЗЖБИ-1», АО «ЖБИ-6», АО «ЗЖБИ N 5», 81 КЖИ, Безенчукский ЗЖБИ-8 ИСК, Похвистневский ЗЖБИ, Тольяттинский ЗЖБК и др.), что позволило обеспечить стабильный выпуск изделий с заданными техническими свойствами. Причем наружные ограждающие конструкции, изготовленные на этом бетоне, удовлетворяли новым требованиям по теплозащите и энергосбережению ( в соответствии с Изменениями N 3 СНиП II-3-79* на первом этапе энергосбережения). Была также доказана эффективность применения керамзитопенобетона при вертикальном формовании наружных стеновых панелей на Тольяттинском заводе коттеджей, возведении монолитных коттеджей АОЗТ «ЮВИРА» в г. Самаре и монолитных многоэтажных жилых зданий АО «Монолитспецстрой» в г. Иошкар-Оле. В 1997-1998 гг. проводилась работа для Тольяттинской ТЭЦ по замене дорогостоящей и трудоемкой наружной теплоизоляции паровых котлов из совелита на изоляцию из керамзитопенобетона. Доказана также долговечность и экологическая безопасность керамзитопенобетона.
Наметившийся сегодня повальный переход на выпуск трехслойных панелей связан с рядом трудностей. Предлагаются решения трехслойных железобетонных панелей с гибкими связями, железобетонными ребрами или шпонками. В этих панелях утепляющим слоем являются минераловатные, стекловолокнистые или полимерные теплоизоляционные материалы. Однако конструкция данных панелей предполагает их высокую теплотехническую неоднородность, составляющую в соответствии с нормами порядка 0,5-0,75. Это обусловлено значительными теплопотерями в зоне стыков, связей, шпонок и ребер жесткости. Использование отечественных теплоизоляторов в качестве среднего слоя в трехслойных панелях является также весьма проблематичным. Так, минераловатные и стекловолокнистые материалы обладают высокой гигроскопичностью и при увлажнении значительно снижают свое термическое сопротивление. Удаление же влаги в случае ее попадания во внутреннюю полость панели практически не представляется возможным. Отечественные полимерные теплоизоляторы являются пожароопасными и при горении выделяют опасные для здоровья человека вещества, что вызывает необходимость устройства в панелях специальных несгораемых вкладышей. Кроме того, в процессе эксплуатации неизбежно происходит старение полимера, а оценить состояние находящейся внутри изделия теплоизоляции практически невозможно. Вполне вероятно выделение вредных для здоровья человека веществ в процессе эксплуатации здания и деструкции полимера.
Производство этого типа панелей отличается более высокими затратами труда и расходом арматурной стали по сравнению с однослойными. Кроме того, оно продолжает оставаться многооперационным, что обусловливает повышенные стоимостные и трудовые затраты, приводит к увеличению расхода металла на 25-30% и повышению марки бетона наружных слоев панели до М200.
Следует отметить, что важным конструктивным элементом наиболее эффективной трехслойной стеновой панели являются гибкие связи, которые обеспечивают совместную работу облицовочного и несущего слоев, фиксацию слоев утеплителя по площади стены и ряд других функций. Долговечность таких ограждающих конструкций непосредственно связана с долговечностью гибких связей. Большой опыт применения трехслойных панелей в Западной Европе, США и Канаде показывает, что долговечность этих конструкций обеспечивается только при использовании связей из нержавеющей стали (в отдельных случаях применяются оцинкованные связи). Однако такие связи имеют очень высокую стоимость. При расходе стали на 1м2 стены порядка 1,2 кг стоимость гибких связей составляет около 30% от стоимости стенового материла или около 50% от стоимости утеплителя, что приводит к удорожанию стеновой панели в 2-3 раза.
В развитых странах Европы и Америки в настоящее время налажен выпуск широкой номенклатуры теплоизоляторов, отвечающих самым высоким критериям по комплексу строительно-технологических и эксплуатационных показателей и полностью пригодных для внутреннего слоя трехслойных панелей. В качестве примера можно привести производимый в США фирмой «Dow Chemical Co» голубой экструзионный пенополистирол (ХРS). Однако стоимость такого пенополистирола составляет порядка 300 долларов США за 1 куб. м.
Отечественное производство экструзионных пенополистиролов только зарождается. Так, фирмой «Экспол» и Решским химическим заводом осваивается производство экструзионного пенополистирола (ЭППС), по своим качествам не уступающего зарубежным аналогам. В настоящее время АО «Химический завод» (Свердловская область) на основе полистирола АО «Салаватнефтеоргсинтез» ведет работы по организации производства экструзионного пенополистирола (ЭППС), который будет соответствовать по показателям известному XPS (США).
Приведенные выше сведения указывают на несомненную дороговизну высококачественных и долговечных трехслойных панелей, а также практически полное отсутствие в стране отечественных эффективных теплоизоляторов, полностью удовлетворяющих требованиям, предъявляемым для внутреннего слоя трехслойных панелей.
На наш взгляд, вводимые для второго этапа энергосбережения нормы с 01.01.2000 г. несколько завышены, исходя из реальных возможностей стройиндустрии. Заводы в своем большинстве не готовы к переходу на выпуск трехслойных панелей, да и в стране нет утеплителей, полностью пригодных для внутреннего слоя этих панелей.
В свете выше сказанного панели из керамзитопенобетона на особо легком керамзите будут иметь сравнительно низкую стоимость и обеспечивать высокую технологичность процесса их изготовления. Отсутствие дефицита керамзита позволит решить проблему массовости производства панелей. Переход на выпуск керамзита с насыпной плотностью 150-200 кг/м³ не должен вызвать особых проблем, т.к. в настоящее время разработано достаточно много технологий (различные способы подготовки сырья, введение специальных добавок и др.), позволяющих производить облегченный керамзит практически из любого вида глинистого сырья.
Передовой зарубежный опыт показывает, что керамзитовые заводы развитых стран, например, заводы, возводимые фирмой «Интема» (Германия), рассчитаны на производство не одного вида керамзита, как это делается у нас, а выпускают несколько видов керамзита (до 2-х, 3-х и более) с учетом требований заказчика и предполагаемой областью применения керамзита, например, в эффективных теплоизоляционных и несущих конструкциях. Так, производимый на заводах этой фирмы керамзит с насыпной плотностью 220, 440 и 660 кг/м³ рассчитан на применение в теплоизоляционных, конструкционно-теплоизоляционных и конструкционных бетонах широкой номенклатуры с маркой по прочности от М50 до M500 (при условии, что прочность керамзита при сдавливании в цилиндре составляет не менее 13% от марки бетона). При таком комплексном подходе стоимость керамзита становится сопоставимой со стоимостью привозного щебня, а в ряде случаев и дешевле за счет снижения транспортных расходов. Следует отметить, что многие регионы страны не имеют качественного природного крупного заполнителя и доставка его из удаленных областей значительно повышает его стоимость.
При широком использовании керамзита в конструкционно-теплоизоляционных и конструкционных бетонах снижаются затраты на монтаж изделий на строительной площадке, существенно уменьшаются нагрузки на здание, что позволяет удешевить расходы на возведение фундамента и т.д. Нашим керамзитовым заводам следует перенять этот зарубежный опыт и перейти на выпуск широкой номенклатуры керамзита как по насыпной плотности, так и по фракционному составу.
В нашей стране имеется положительный опыт применения керамзитобетона в качестве эффективного утеплителя. Так, в 1962 г. было предложено применить жесткий плитный утеплитель из крупнопористого бетона при строительстве Самарского завода координатно-расточных станков. Высокая точность изготовления изделий на этом заводе потребовала чрезвычайно жестких ограничений на возможные колебания температуры внутри помещений, составляющие 0,4ºС. Применение плитного утеплителя из крупнопористого керамзитобетона (на керамзите с насыпной плотностью 250 кг/м³) для теплоизоляции покрытия цеха позволило отказаться от использования импортных дорогостоящих материалов и получить необходимые температурные параметры в помещениях завода.
Довольно значительное место, в частности в Самарской области, нашло применение крупнопористого керамзитобетона в качестве теплоизоляционного слоя в плитах покрытий (ПНС, ПКЖ и др.), изготовляемых в едином технологическом цикле непосредственно на заводе. Это позволило в значительной степени повысить производительность труда и снизить стоимость строительства при возведении различных промышленных объектов.
Этот опыт показывает, что на основе особо легкого керамзита можно наладить выпуск эффективных жестких плитных утеплителей.
Таким образом производство особо легкого керамзитового гравия следует признать весьма эффективным для изготовления теплоизоляционных конструкций.
Другим направлением развития керамзитовой промышленности может стать широкое использование керамзита в конструкционных бетонах.
Так, имеется давний опыт комплексного использования керамзитобетона (практически все конструкции здания изготавливаются из керамзитобетона) при строительстве жилых домов. Одним из лучших примеров комплексного применения керамзитобетона в жилищном строительстве являются типовые проекты серии 99 ЦНИИЭПжилища, в состав которой входят одно- и двухэтажные дома для села и пяти-, девяти-, шестнадцати- и двадцатипятиэтажные жилые дома для города. Комплексное применение керамзитобетона обеспечивает снижение трудоемкости на 8%, транспортных затрат на 30%, стоимости на 2-5%, расхода арматурной стали и бетона на 10%. Положительный опыт применения керамзитобетона накоплен и при строительстве монолитных высотных жилых домов, монолитного элеватора, проектировании, изготовлении и возведении промышленных зданий полностью из керамзитобетона и др.
Возможен вариант производства особо тяжелого керамзита («керамдора») при пониженных на 200-300ºC температурах с насыпной плотностью порядка 900 кг/м³ и более. Такой керамзит будет вполне конкурентоспособным за счет экономии расхода энергии на его производство по сравнению с привозным природным щебнем. Область его применения — дорожное строительство, несущие конструкции из железобетона и др.
Кроме технологических и экономических преимуществ, керамзит по сравнению с природным щебнем обладает рядом достоинств:
- улучшенным сцеплением растворной части бетона с заполнителем за счет более глубокого проникновения цементного камня в поры керамзитовых гранул и гидравлической активности керамзита, что повышает долговечность, прочность и химическую стойкость бетона. Это подтверждается опытом применения керамзитобетона в полах животноводческих помещений, лотках теплотрасс, фундаментах и др.;
- пониженной средней плотностью при сохранении основных строительно-эксплуатационных свойств, что уменьшает среднюю плотность бетона и позволяет облегчить конструктивные элементы здания;
- сырьевая база для производства керамзита практически не ограничена, а добыча качественного щебня для Центральной России производится только на Урале.
Вывод
Необходимо пересмотреть политику производства керамзита, т.е. не останавливать керамзитовые заводы, а переориентировать их на новые задачи, связанные с ориентацией заводов на выпуск особо легкого керамзита (для изготовления эффективных ограждающих конструкций, плитных утеплителей и т.п.), тяжелого и прочного керамзита (для производства несущих конструкций, строительства дорог, монолитных зданий и сооружений и т.п.). Это повлечет за собой необходимость в пересмотре нормативно-технической базы производства керамзита (ГОСТов, СНиПов, технологических регламентов и др.).
Выполнение комплекса этих мероприятий позволит в значительной степени снять вопрос о материалах, пригодных для выпуска современных ограждающих и несущих конструкций, и снять с повестки дня вопрос о дефиците эффективных материалов для строительства.
Авторы: Б.Комиссаренко, профессор, член-корреспондент Российской академии технологических наук / А.Чикноворьян, доцент, кандидат технических наук, Самарская государственная архитектурно-строительная академия