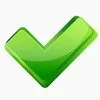
Технология строительной керамики на предприятиях малой мощности (Республика Татарстан)
Доля малых предприятий в промышленности стеновых материалов по данным 1998 года составляет 84%. Износ основных фондов в подотрасли кирпичного производства составляет более 40%, около 60% предприятий являются убыточными (А.И. Елфимов. Концепция, развития производства и рынков стеновых материалов в рамках среднесрочной программы социального и экономического развития Российской Федерации. «Строительные материалы», 1998, N 6).Несмотря на планируемый ввод нескольких импортных линий по производству облицовочных стеновых материалов и при этом практическое отсутствие инвестиций, в ближайшие годы ожидать значительного обновления основных фондов и ликвидации нехватки керамических стройматериалов по стране, особенно лицевого кирпича, не приходится.
В этих условиях возникшие проблемы могут быть реально решены на предприятиях малой мощности.
В нашей стране в последнее время наметилась тенденция к строительству технологических линий малой мощности — до 3 — 5 млн. шт. условного кирпича в год. Это связано в основном с освоением мелких месторождений глин в районах и глинистых отвалов от строительства различных производств, а также установка керамических линий на предприятиях другой отрасли промышленности для обеспечения нужд местного строительства. Эти производства базируются в основном на отечественных или индивидуальных разработках малотоннажного оборудования.
Примером такого решения могут служить линия полусухого прессования кирпича с комплектом оборудования от ВНИИстрома им. П.П.Будникова, внедренная на предприятии ОАО «Завод ЖБИ — 3» (г. Казань); линия полусухого прессования с оригинальными технологическими решениями и индивидуальными разработками оборудования, работающая на глинистых отвалах КамАЗа и построенная специалистами кооператива «Иремель» в г.Набережные Челны Татарстана.
На казанской линии с проектной производительностью в 3 млн. шт. условного кирпича в год получен кирпич марок 175 — 250 и морозостойкостью значительно более 50 циклов, с большими (порядка 3 — 4 МПа) показателями прочности на изгиб, что не характерно для кирпича полусухого прессования.
Опробована технология пластического формования кирпича, черепицы и получены образцы с хорошими физико-механическими показателями.
В данном случае высокие физико-механические показатели керамического материала достигнуты были благодаря тщательному подбору места разработки обширного месторождения, где химико-минералогические особенности глинистого сырья позволили прогнозировать хорошее качество изделия при отработанной для него технологии.
Технология полусухого прессования была заложена исходя из соображений экономической целесообразности организации производства малой мощности по получению керамических изделий, в данном случае лицевого кирпича, черепицы, изразцов (А.В.Беляков, В.С.Бакунов. Стабильность качества изделий в технологии керамики. «Стекло и керамика», 1998, N 2).
В качестве сырья был выбран мощный пласт близлежащего к предприятию Калининского месторождения Татарстана, представляющего собой пылеватый суглинок с содержанием 49 — 52% глинистой, 38 — 42% пылеватой и 8 — 12% песчаной фракции. Глина умеренно-среднепластичная, с низким содержанием мелких включений, дисперсная, среднечувствительная к сушке.
Технологическую особенность суглинка обуславливает присутствие в песчаной фракции до 20% угля (около 2% от общей массы глины).
В процессе испытания глинистого сырья на технологической нитке полусухого прессования была отмечена значительная корреляция свойств керамического материала от предыстории его изготовления и незначительных колебаний параметров технологического процесса, так называемых точек бифуркаций (А.В.Беляков, В.С.Бакунов. Стабильность качества изделий в технологии керамики. «Стекло и керамика», 1998, N 2; А.В.Беляков, Е.А.Брыгина. Локальные уплотнения при спекании керамики и воспроизводимость структуры. «Стекло и керамика», 1998, N 10), выявление и управление которыми стало основной технологической задачей.
Получение керамического материала стабильного качества потребовало от технологов выявления и создания условий для снижения степени неравновесности технологических процессов, которые бы привели к созданию диссипативных структур при конкретных условиях внешнего воздействия.
Известно, что технологические свойства глинистого сырья и формуемого из него изделия-сырца определяются взаимопревращениями коагуляционных и конденсационных структур, а свойства керамики — образующимися при обжиге кристаллизационными образованиями (А.В.Беляков, Е.А.Брыгина. Локальные уплотнения при спекании керамики и воспроизводимость структуры. «Стекло и керамика», 1998, N 10; Г.И.Масленникова, Ю.Т.Платов. Процесс образования фарфора в присутствии добавок. «Стекло и керамика», 1998, N 2). Все эти преобразования сопровождаются массопереносом, играющим основную роль в технологии керамики, и значительно различаются для каждой категории глинистой композиции. При этом важна скорость нарастания массопереноса, определяющая степень неравновесности реакции системы на внешние воздействия и оказывающая основное влияние на период формирования керамического черепка, и как результат — конечный период обжига и производительность всей линии.
На основании этих теоретических соображений была поставлена работа по балансировке технологического процесса. Отслеживание процесса формирования керамического материала необходимого качества позволило технологам для имеющегося у них сырья и заложенной технологии определить ключевые точки бифуркации на основных стадиях технологического процесса и способы управления поведением системы в них, т.е. по мере возможности довести имеющийся техпроцесс до теоретически необходимого.
Изучение деформационного поведения различных видов керамического черепка пластического и полусухого формования показали, что последний обладает наиболее совершенной кристаллизационной структурой. Это выражается повышенными показателями прочности на сжатие (П.П.Будников. Химия и технология строительных материалов и керамики. М., «Стройиздат», 1965 г.) и объясняется различием в механизме формирования оптимальной коагуляционно-кристаллизационной структуры исходного изделия-сырца при переходе от пластического формования к полусухому и закрепленной при обжиге.
При полусухом прессовании в диапазоне 5 — 6% влажности имеет место практически однофазное (псевдоконденсационное) твердение. При жестком пластическом формовании практически реализуется однофазное коагуляционное состояние глиняной структуры, причем возрастание доли псевдоконденсационной фазы с увеличением давления в интервале двухфазного состояния, укладывающегося во влажностный технологический интервал 9 — 12% полусухого прессования, реализует как бы самопроизвольное подсушивание массы.
Именно этот механизм формирования структуры материала наблюдался, вероятнее всего, в нашем случае, поскольку особенности сырья вынуждали проводить прессование изделия в диапазоне влажности пресс-порошка, лежащих в пределах 9,5 — 11% и высоких давлениях прессования.
Другими словами, учитывая специфику сырья при использовании способа полусухого прессования, реализовался механизм жесткого формования с образованием смешанной коагуляционной структуры, дающей при правильно проведенном техпроцессе повышенные показатели прочности на изгиб и сжатие. Достигается приближение к идеально организованной так называемой диссипативной структуре высокой плотности, дающей после обжига образцы с высокой морозостойкостью, т.е. достаточно идеальной в нашем случае структуре.
Это позволяло при соблюдении технологических параметров получать кирпичи марок 200 — 250 с морозостойкостью значительно выше 50 циклов.
Незначительные отклонения внешних воздействий от необходимых приводили к резкому падению того или иного показателя качества изделия, в первую очередь по прочности на изгиб при высоком сжатии и наоборот.
Нестабильность качества керамики определяется наличием неоднородностей структуры, ее мультифрактальным характером (А.В.Беляков, В.С.Бакунов. Стабильность качества изделий в технологии керамики. «Стекло и керамика», 1998, N 2; В.С.Иванова, А.С.Баланкин, И.Ж.Бунин и др. Синергетика и фракталы в материаловедении. «Наука», М., 1994), где под фракталом понимают структуру, состоящую из частей в том или ином приближении подобных целому.
Исходя из вышеизложенного, на предприятии был выбран способ переработки глиномассы. Была убрана стадия грануляции массы перед сушкой в шнековом прессе и заменена простым дроблением и смешением глиномассы.
Это позволило избавиться от упругих деформаций, заложенных ранее при грануляции массы, и добиться уменьшения растрескивания сырца при ускоренном технологическом периоде формования и обжига без значительного периода усреднения сырца для релаксации внутренних напряжений, по локальным уплотнениям которых перемещаются трещины (А.В.Беляков, Е.А.Брыгина. Локальные уплотнения при спекании керамики и воспроизводимость структуры. «Стекло и керамика», 1998, N 10).
Для сформованного из предварительно гранулированной массы пресс-порошка изделия необходимо было соблюдать специальные условия усреднения (высокое давление прессования, влажность атмосферы и время усреднения, определенный грансостав пресс-порошка).
Проведенные исследования позволили в производстве отказаться от излишней операции по переработке сырья и ограничиться дроблением и простым перемешиванием глиномассы. Вероятно, влажный пресс-порошок, полученный из дробленой глины, содержит подобно массе при жестком формовании значительную долю конденсационной фазы, не подверженной разупорядочению в естественных условиях, без применения деформирующих напряжений.
Большее содержание топлива в сырье позволило проводить обжиг при температурах в пределах 870 — 910 ºС. В результате эксперимента по скоростному обжигу керамического материала в пределах 12 — 16 часов был получен кирпич марки 250 с хорошим внешним видом. Было отмечено, что длительная выдержка при температурах 200 — 600 ºС, особенно в присутствии паров воды, приводит к перекристаллизации сопровождающейся катастрофической потерей прочности (А.В.Беляков, В.С.Бакунов. Создание прочных и трещиностойких структур в керамике. «Стекло и керамика», 1998, N 1), исчисляемой для кирпича в несколько марок вниз, визуально проявляющейся в получении рыхлого, глухого черепка. При быстром спекании практически исключается влияние исходной структуры (локальных уплотнений при формовании и сушке), а увеличивающаяся степень неравновесности процесса в этих условиях приводит к уменьшению размеров элементов диссипативной структуры и получении керамического черепка мелкокристаллической структуры (А.В.Беляков, Е.А.Брыгина. Локальные уплотнения при спекании керамики и воспроизводимость структуры. «Стекло и керамика», 1998, N 10; В.С.Иванова, А.С.Баланкин, И.Ж.Бунин. Синергетика и фракталы в материаловедении. «Наука», М., 1994), что проявляется в высокой прочности керамического черепка. Кроме того, известно (И.А.Альперович. Керамические стеновые и теплоизоляционные материалы в современном строительстве. «Строительные материалы», 1997, N 6), что зологлиняные дисперсные системы, к которым принадлежит исследуемое сырье, при повышении скорости нагревания сохраняют низкий коэффициент термического линейного расширения в области упругохрупкого состояния в диапазоне температур 500 — 900 ºС, благодаря чему при скоростном обжиге не возникает разрушающих напряжений и не образуются трещины на поверхности кирпича.
Все вышеизложенное открыло хорошие перспективы по повышению производительности всей технологической линии. Это особенно важно для малотоннажных производств, таких, как линия по производству кирпича полусухого прессования на заводе ЖБИ-3 с перспективой получения 3 млн. штук условного кирпича в год, себестоимость которого уже заложена высокой.
Таким образом, на неспециализированном предприятии керамической промышленности ОАО «Завод ЖБИ-3» была более или менее осуществлена технологическая задача — получение керамического кирпича высокой марочности по прочности и морозостойкости на линии малой мощности, скомплектованной из экспериментального оборудования отечественной разработки. Решены достаточно сложные технологические задачи, особенно учитывая специфику сырьевого материала и аппаратурного оформления технологической нитки — это создание условий для снижения степени неравновесности процессов в областях неустойчивых состояний и направленное создание структур, используемых системой в качестве диссипативных при конкретных условиях технологического процесса.
Результатом работы было получение образцов лицевого кирпича высокой марочности.
Таким образом, развитию направления в керамической промышленности по производству кирпича на линиях малой производительности требуется решение основного вопроса: как восполнить отсутствие производимого промышленностью оборудования для линий такой малой производительности. Этой проблемой начали заниматься на Украине в центре керамического машиностроения бывшего СССР. Есть разработки прессового оборудования и интересные решения по печам для скоростного обжига с использованием пока что комплекта приборного оформления и технологических решений зарубежных фирм. Появились интересные предложения и разработки оборудования в Сибири (г. Омск, фирма «ШЛ»), Белоруссии (г. Могилев, фигурный кирпич, черепица), в г.Пензе (УНИТРОН) и др.
На базе отдельных машиностроительных предприятий и заводов авиационного, военного комплекса с привлечением научно-инженерного персонала строятся линии с оригинальными технологическими решениями и разработками оборудования. Примером такого варианта может служить кооператив «Иремель», построенный специалистами КамАЗа в Татарстане.
Таким образом, организация производства строительных керамических материалов малой производительности базируется на частных разработках отдельных коллективов или лиц, часто работающих в других отраслях промышленности, и исполненных в единственном варианте.
В настоящий момент необходимо объединить отдельные решения и наладить производство наиболее зарекомендовавшего себя оборудования. Объединив зарубежный и отечественный опыт с насущными проблемами сегодняшней действительности, найти варианты реальной на сегодняшний момент организации эффективного производства строительной керамики малой мощности.
Полезно организовать обсуждение этой тематики и из накопленного опыта предложить наиболее экономически эффективные варианты технологических схем производств для каждого базового типа сырья. Это позволило бы организаторам легче ориентироваться в выборе типа производства, оценить свои возможности для строительства той или иной технологической линии в зависимости от имеющегося в наличие сырья, тем самым способствовать расширению производства керамических стройматериалов по стране.
Автор: И. Женжурист, к.т.н., зав.лабораторией кирпичного производства ОАО «Завод ЖБИ-3»